The stone floor is the upper floor of the steam mill, where the millstones where located. It is a complex structure with four layers of planks, some bolted together. At some time in the past the original roof failed, wet rot and wood worm took hold and eventually part of the floor collapsed, leaving a large hole. As a result the floor had been designated off limits.
In the last quarter of 2014 two small areas of the floor were repaired by the volunteers with the support of ECC and a grant from Maldon District Council. This allowed us to go onto the floor with care. Over 2015 and 2016 an extensive survey of the floor structure was undertaken and a series of scale drawings produced. At first we tried to get a heritage building contractor interested in working with us to repair the floor. However, those we approached firstly expressed interest, then eventually stopped returning our calls.
In late 2016 further searching of the internet identified Dr Joe Bispham as a Historic Buildings Consultant, and even better one of our volunteers, Richard Rowsell, knew him. We made contact and Dr Bispham visited the mill and agreed to help us develop a plan. With his help we consulted Maldon District Council’s Heritage Planning officers and got agreement to repairing the floor subject to further consultation about the details.
In April 2017 volunteers from the Beeleigh Mill Restoration Group started to strip back the timbers of the Stone Floor to expose the main beams for inspection and ultimate repair by specialists in the field.
The Stone Floor is supported off a grid of major beams. Beam C runs the length of the room, while Beams A, D and B are supported by Beam C at one end and are set into the back wall of the mill at the other. Beams DA and DB lie between beams A and D and D and B respectively. The Beams A, B and C form a perimeter around the mill stone positions. Outside of these beams there are joists and floorboards. The joists are set into the beams with mortice and tenon joints and set into the wall in pockets.
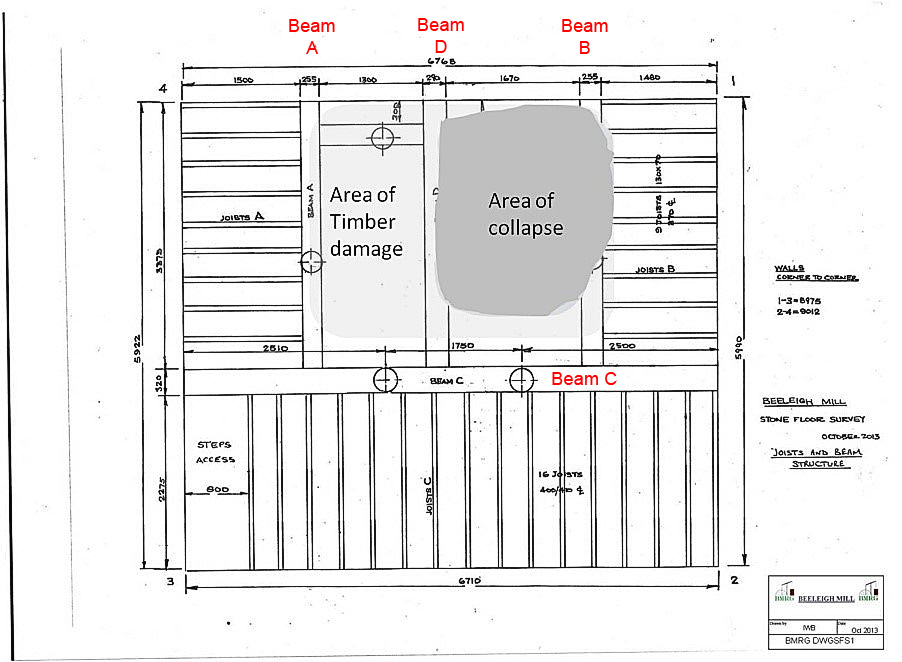
The major hole in the floor was located between Beams D and B. Beam DB had been severely damaged, Beam D had major damage and Beam B some damage. Joists B1, B2 and B3 had become disconnected from Beam B and were supported by a prop for safety. Mill stone position 1 had completely disappeared and Position 2 had some damage.
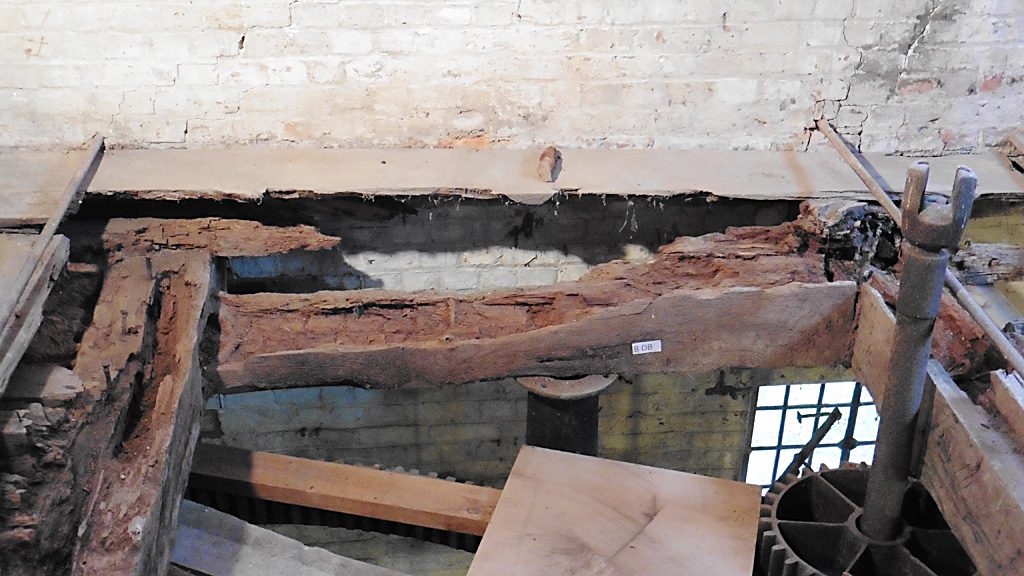
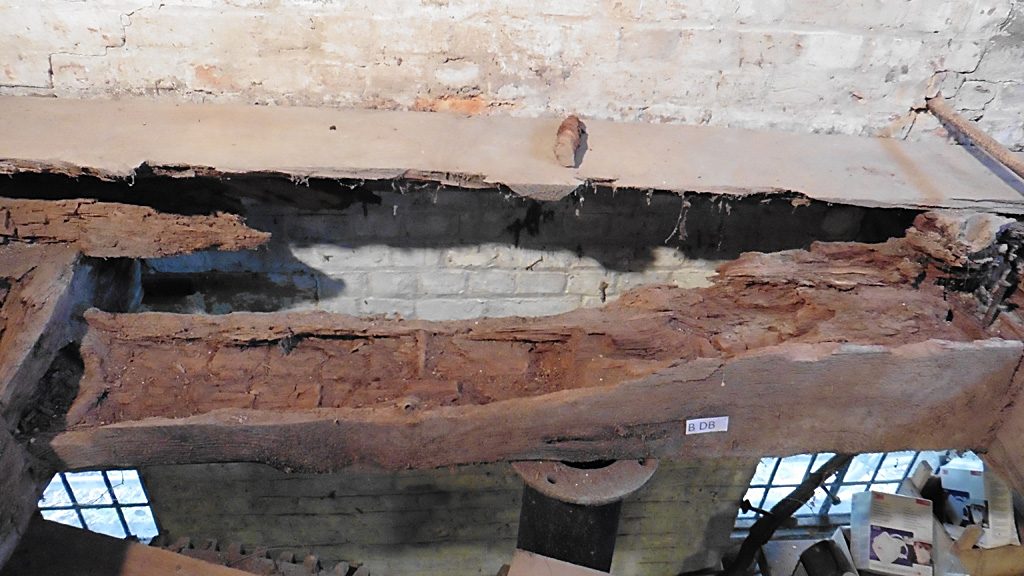
After each layer of timber was removed the exposed timber layer was surveyed and the data added to a 2D CAD drawing using “Draftsight” software. It quickly became apparent that the second layer of timber, the kerbs, had been badly affected by woodworm and some of these timbers crumbled to dust when disturbed. Those that didn’t were carefully removed and placed in storage. Subsequently each piece was measured, labelled where appropriate and photographed for future reference.
In early August the bottom layer of timber was reached and planks 1 to 13 were removed. The condition of these planks was much worse than was believed from the initial survey work. These had to be replaced.
Dr Bispham visited site in mid August with a scaffolding contractor to establish how to create the required access to the beams for the next phase of the project. A Maldon District Council Conservation Officer also visited the site on the same occasion in order to see progress.
We believed that the wood the floor had been constructed largely in Baltic Pine. However, the Conservation Officer pointed out the different appearance and degree of insect damage to the kerbs forming the second layer of timber and suggested these could be of a different species. We concluded they were most likely made of Elm and as this is very difficult to obtain, we proposed replacing them with oak.
In September 2017 a scaffold platform was erected about 600mm below the beams of the stone floor. This allowed close access to the beams, which had been fully exposed by the previous removal of floor timbers. The installation of this platform allowed Dr Bispham, to inspect the beams and in consultation with Tim Howson, Maldon District Council Conservation Officer, to work out how best to approach the repair of the beams.
The plan agreed was as follows:
Beam no.B
The section needing repair was approximately 1.5-1.8m long.
The repair method was to cut into the existing beam and scarf in two new sections. The scarfed sections were to be a table scarf with abutments. The new section to the beam to have mortises cut into both faces one side to accommodate the floor joists and the other for the bridging beam.
Beam no.BD.
This required a new bridging beam the same size as the original, with tenons into beam no.D and beam no.B
Beam no. D.
This beam has the vertical shaft attached at approximately 2m from the rear wall.
This beam appeared to be rotten and beetle damaged up to the vertical shaft. It was proposed that this beam was to be removed up to the vertical shaft, the nuts to be removed from the bracket that secures the vertical shaft to the beam and a steel plate to be fixed over the protruding bolts then the nuts re-secured. The new beam was to be a two part beam with a metal flitch. The flitch beam was to be bolted through the first section of timber, through the metal flitch and through a packer (to give width) and then through the final section of beam. The beam was to have the same bearing as the original beam. The face of the beam that connects to the new bridging beam was to be mortised to take the bridging beam. The details of the steel plates and size and position of the bolts were to be agreed with a structural engineer who is a member of the Beeleigh Mill Restoration Group.
Beam no. AD. A section was to be cut from the top of this beam and a new section of timber will be fixed to give the correct thickness.
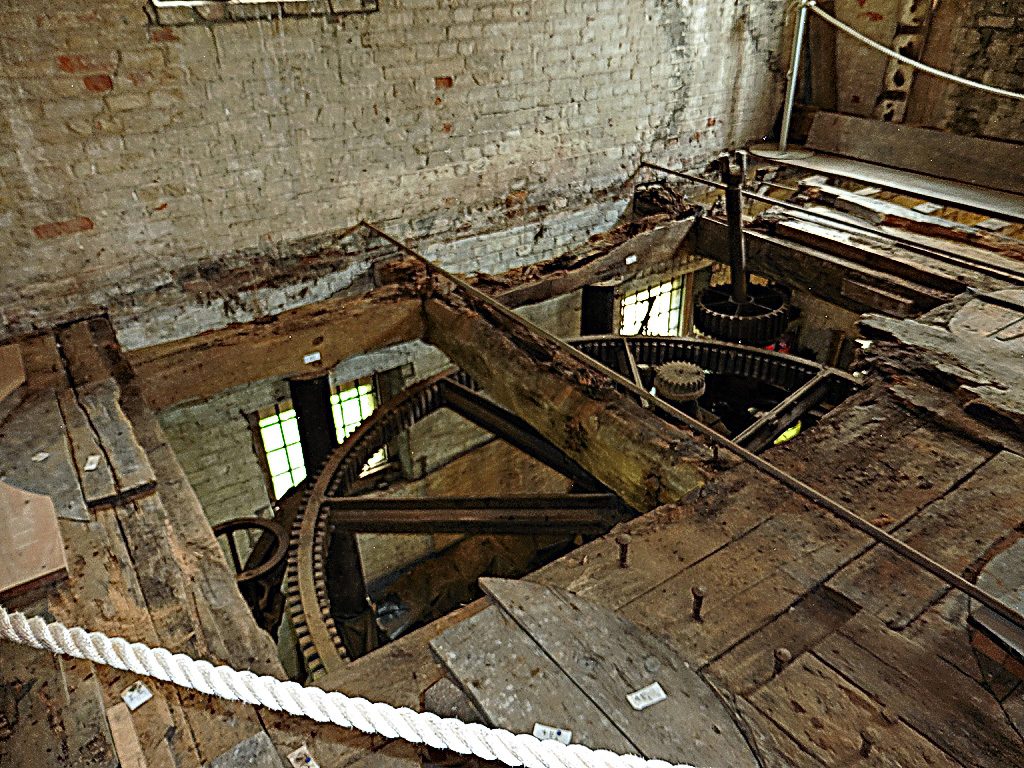
In October BMRG volunteers removed a little more timber to better expose Beam B and also install props to support the Spur Wheel and to lock the vertical shaft in position, regardless of what was done to Beam D.
In early November 2017 Dr Bispham and his team started work. BMRG were pleased to welcome Mr Dale Perrin as part of Dr Bispham’s team. Mr Perrin was undertaking a fellowship course for the Society for the Preservation of Ancient Buildings, one of the supporting organisations for the project and was spending a week with Dr Bispham.
Over four days Dr Bispham stripped back the rotten wood from the beams and found that overall the damage was not as severe as first thought.
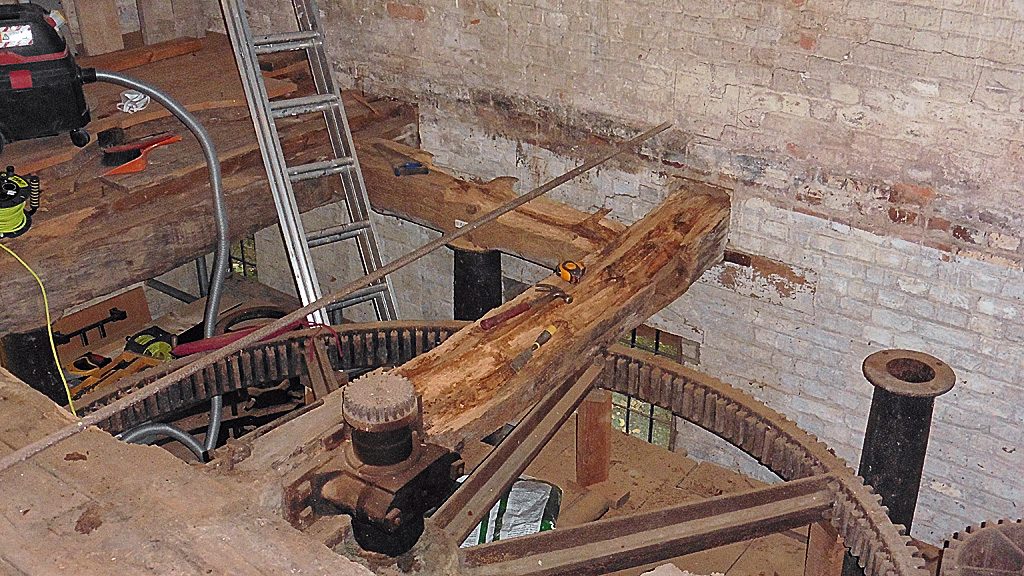
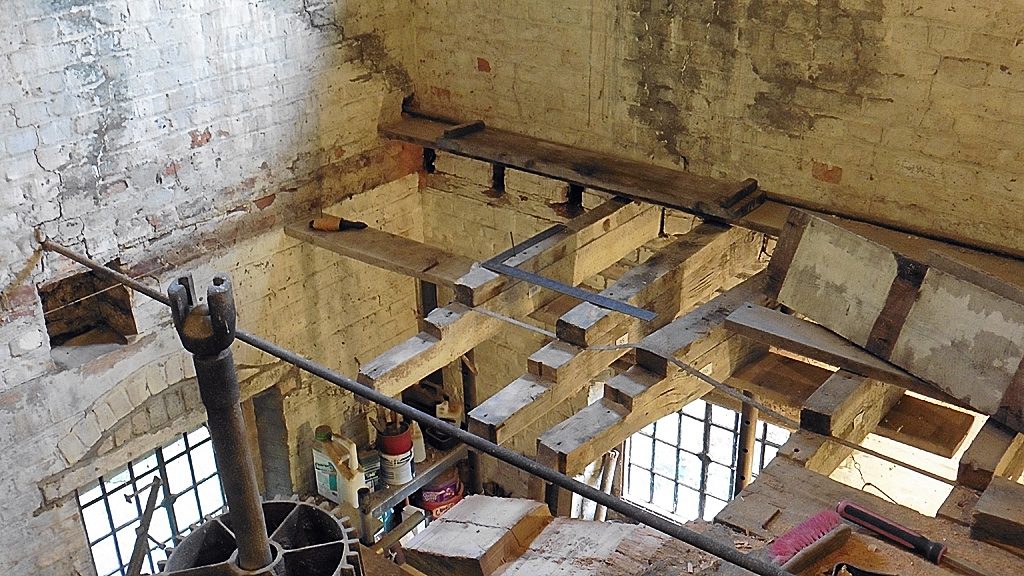
Once the quantity of new timber had been determined and the market checked for availability, the size of available timber of the right quality, and the actual amount of sound wood in Beam D led Dr Bispham to adjust the repair solution to this beam. The plate to be secured by the bolts holding the vertical shaft was enlarged so that all four bolts holding the vertical shaft bracket would be used. Instead of two pieces of timber being used to replace the rotten wood, three pieces had to be used.
Dr Bispham completed the repairs to the beams in mid November (see pictures below).

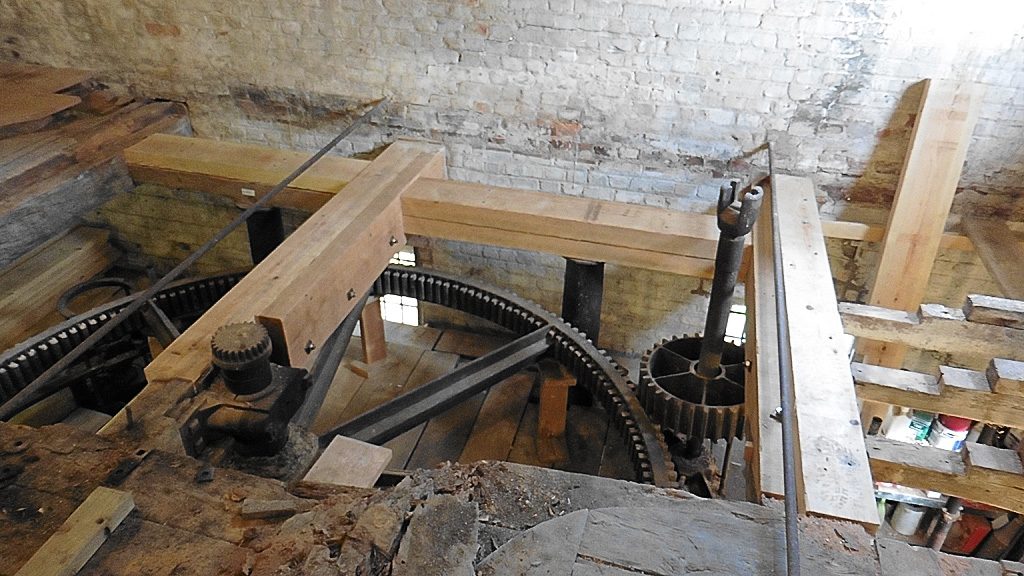
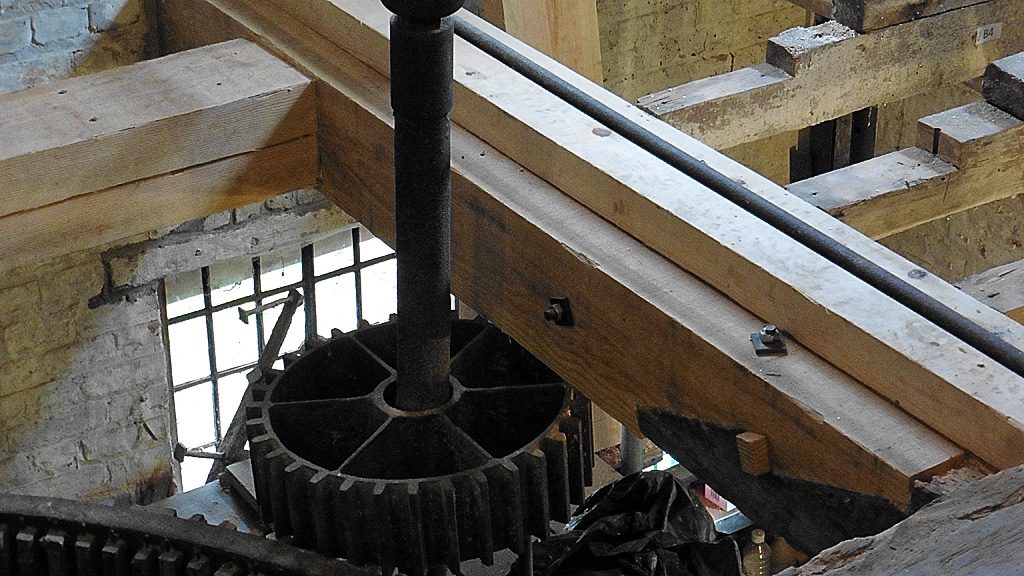
BMRG purchased new Swedish Redwood timber intended for the bottom two layers of the floor structure via Dr Bispham as part of the order he placed for the beam repairs. During the work to remove rotten material Dr Bispham removed some sound wood, from which one could still detect the distinctive “pine” smell of Baltic Pine / Scots Pine and the European Redwood species. A proportion of the new planks of wood have been cut in half by the supplier to produce planks of the right thickness for the second layer of the floor structure.
After Dr Bispham finished the beam repairs volunteers have treated the new timber with a water based boron anti woodworm treatment ready for installation work to commence in January 2018.
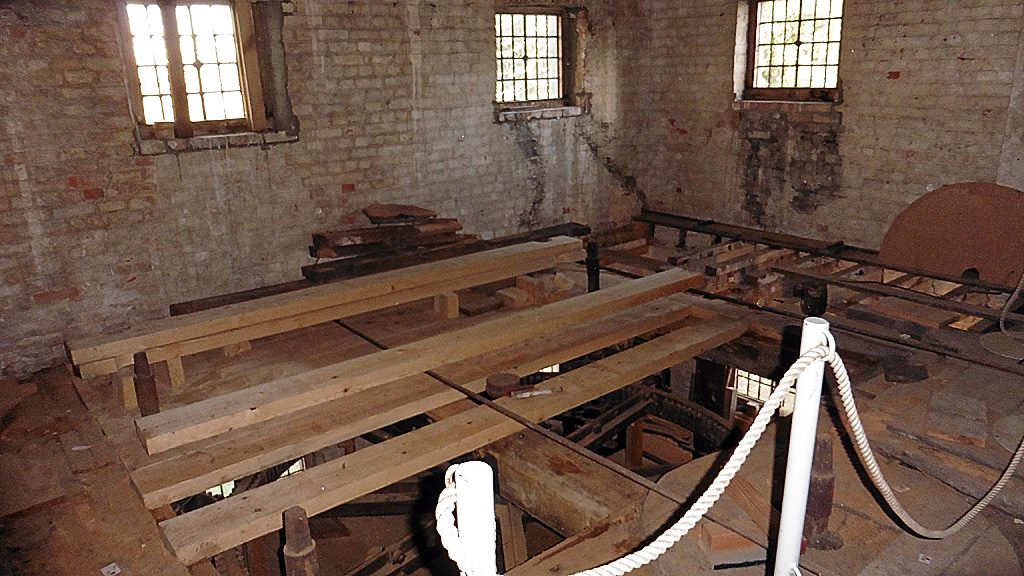
In January 2018 BMRG recommenced work on the floor. Firstly, four more original “base planks” lying between beams A and B were removed due to their condition. In the event it has only been possible to retain one the originals. New planks were then laid between the beams. These were 9in by 3in in section and matched the original timbers. They only needed cutting to length. Where the stone shafts protruded through the timber, two planks were clamped together and a core cutter was used to form a 150mm diameter hole for each stone shaft. The presence of the stone shafts fixed the position of the planks with the holes. It was possible to lay full width planks up to the north wall, but it was necessary to cut a plank lengthwise to complete the layer in line with the vertical shaft and next to the remaining original plank.
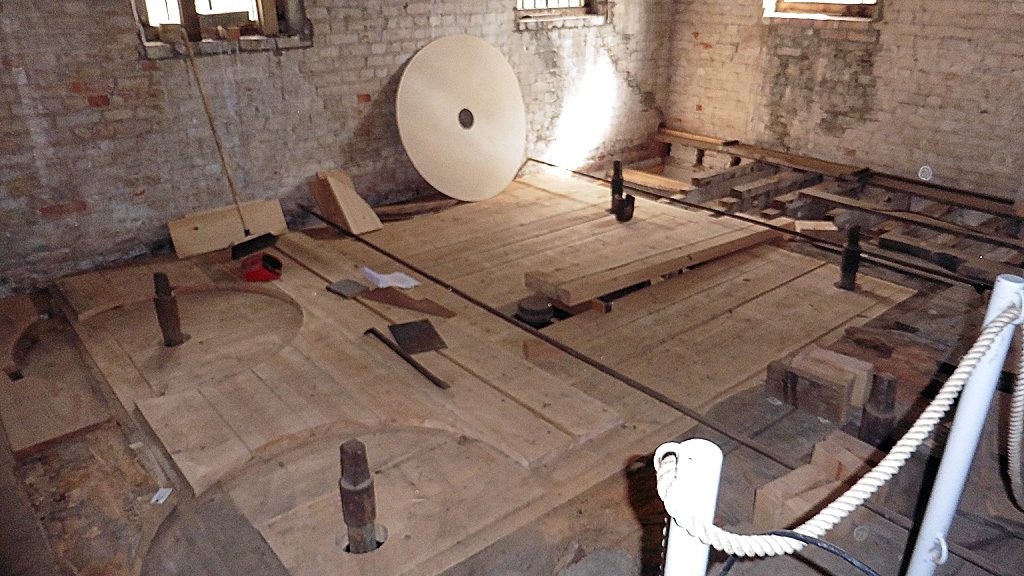
Finally, two planks had to be cut in half where the vertical shaft protruded. This resulted in the planks to the east of the vertical shaft having no support at one end. This was where the original floor had collapsed so there was no evidence of how the original planks had been supported. In consultation with the Maldon Conservation Officer it was decided to make a simple steel bracket which would be sized to be flush with both the top of the planks and with the underside of the floor (See photo 11).
While the bracket was being manufactured at a local steel fabricator BMRG started laying the next layer of timber to the west of beam D. This layer has to be cut to form the recesses for the stones. Some rework has been found to be necessary, so progress has been slow. Once details are finalised the same arrangement will be laid to the east of beam D, an area which had been lost.
In the early phase of consultation the Maldon Conservation Officer had noted that that the layer of kerbs which sit under the floorboards, used to locate the static stones in position, appeared to be made of a different timber from the rest of the structure and it had been agreed that a native hardwood would be sourced for these. Dr Bispham had a quantity of oak surplus to his requirements and he agreed to sell this to BMRG. In February 2018 two volunteers visited Dr Bispham’s workshop with a cutting list and identified which oak planks could be used. Dr Bispham then sourced additional oak planks on behalf of BMRG to enable them to make all the kerbs required.
The next step was to lay the “third layer” planks on the west side of the floor around millstone positions 4 and 5 and east of Beam A. Hardboard templates of the stone recesses have been made and were used to mark out the timber for cutting. The third layer timber has had to be planed to achieve the correct level adjacent to original timber work. Minor repairs have also had to be done to the top face of Beam A.
While work continued on the 3rd layer timbers adjacent to stone positions 4 and 5, volunteers cut pieces of oak plank in order to make kerb C12 which lies to the west of these positions. The kerbs are being made up of a laminate of oak planks to achieve a final thickness of 60mm. The availability of the completed, but unfinished, kerb C12 (see diagram below) allowed final adjustments to the thickness of the 3rd layer planks to be made.
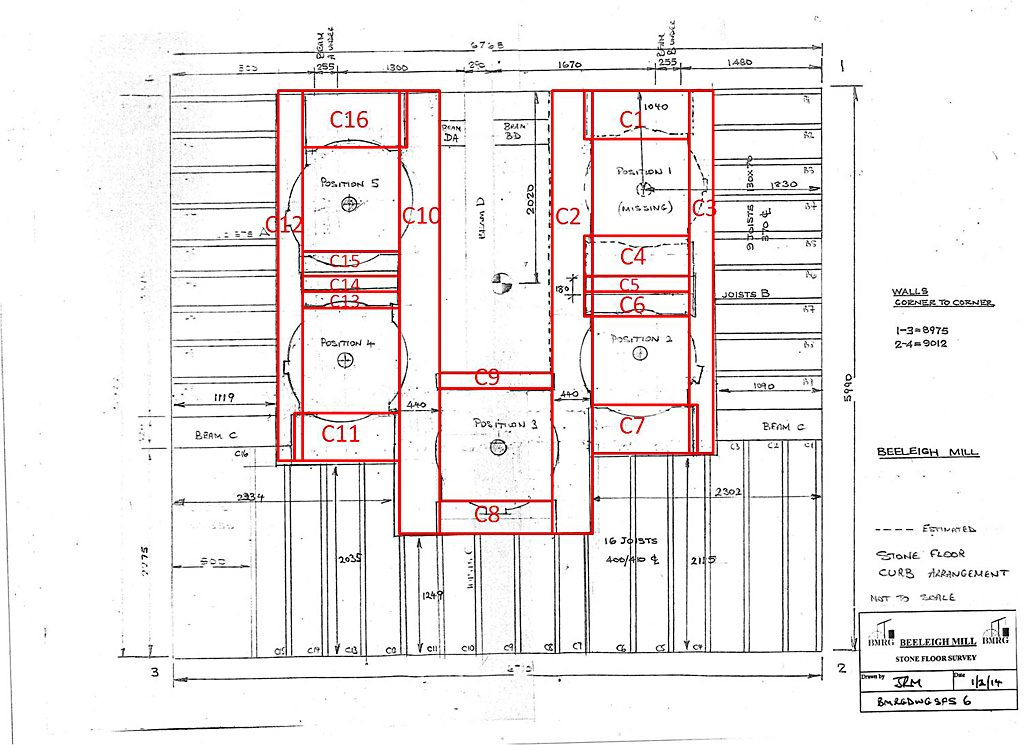
Attention then turned to the two long kerbs C2 and C10.
While these were being assembled floorboards south of position 2 were removed to allow the remains of the original kerb C2 to be removed. At this stage the volunteers found that two base planks under position 3 were not sound enough to be retained. It had been hoped that the timbers here would not need to be disturbed. Fortunately, timber of the right section was available and the two short planks were replaced with new timber. 3rd layer planks were then laid to the west of stone positions 1 and 2 and cut to form the stone recesses. This allowed the prepared planks forming kerb C2 to be cut to length and laid. Again the 3rd layer planks have been planed to achieve the correct levels adjacent to original timbers south of position 3. This process has been repeated for kerb C10.
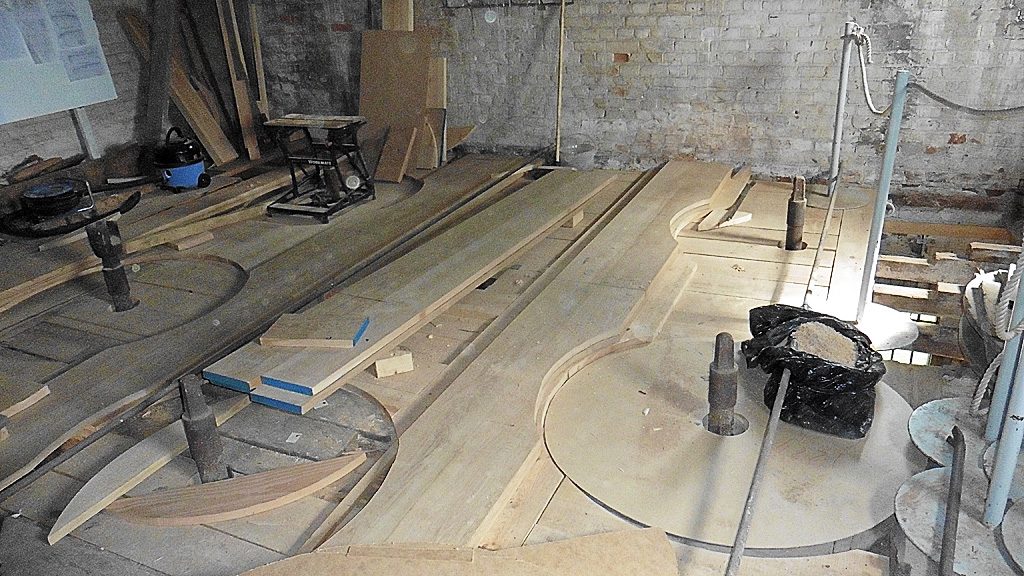
At the start of July work progressed with fitting kerb C12 on the west side of the mill, and then C9 at stone position 3. Meanwhile other volunteers first fitted a baton to Beam B to provide some additional support to the “B” joists at their connections with Beam B. They then installed 3 replacement joists, B1, B2 and B3 on the east side of the floor. The original joists had been severely damaged by worm and rot. Joist B4 was found to have deteriorated where it sat in its pocket in the east wall. Rather than replace the whole joist a new tenon section was made and joined to the original timber using a steel rod to reinforce the connection.
Kerb C12 took longer to complete than expected, due to holidays and difficulties in getting the level of new timbers to match the required levels of the old timber where they butted up against each other. However once the level issue was overcome the connecting kerbs C11, C13, C15 and C16 were made and fitted.
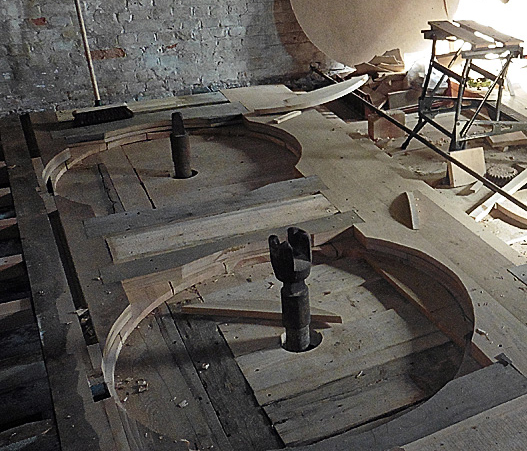
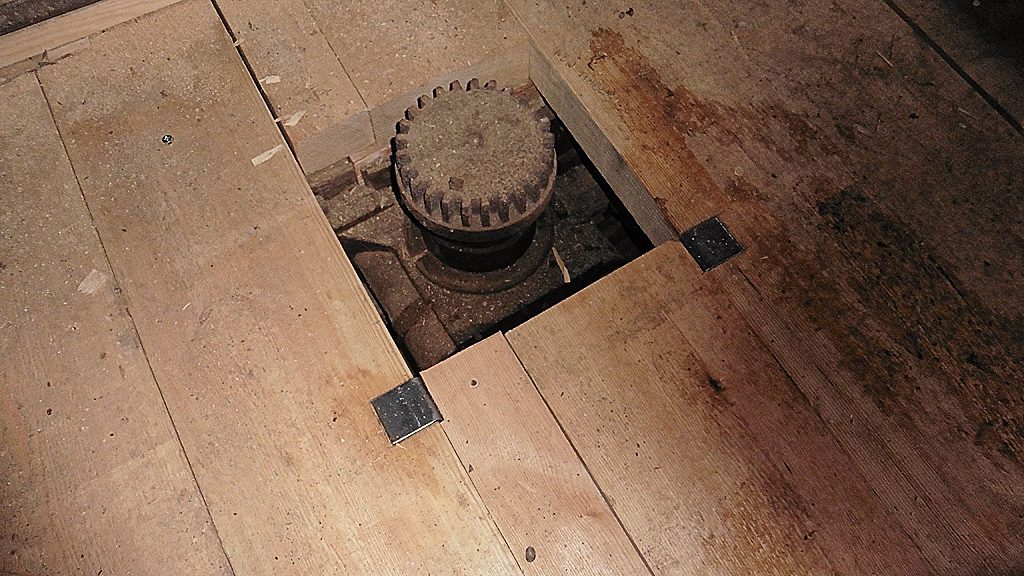
By the end of September the third layer planks were cut and laid around positions 1 and 2 with one more to cut and lay. During October 2018 work continued around Positions 1 and 2, cutting and fitting the cross kerbs that lie between kerbs C2 and C3. Volunteers also cut timber to make and then lay a set of “joists” which lie between kerbs C10 and C2 north of position 3. These “joists” sit on the base planks, are notched to overlap with the 3rd layer planks and have their upper surface at the same level as the kerbs. When the old timbers were stripped back virtually all of the original joists had disintegrated. (see photos below).
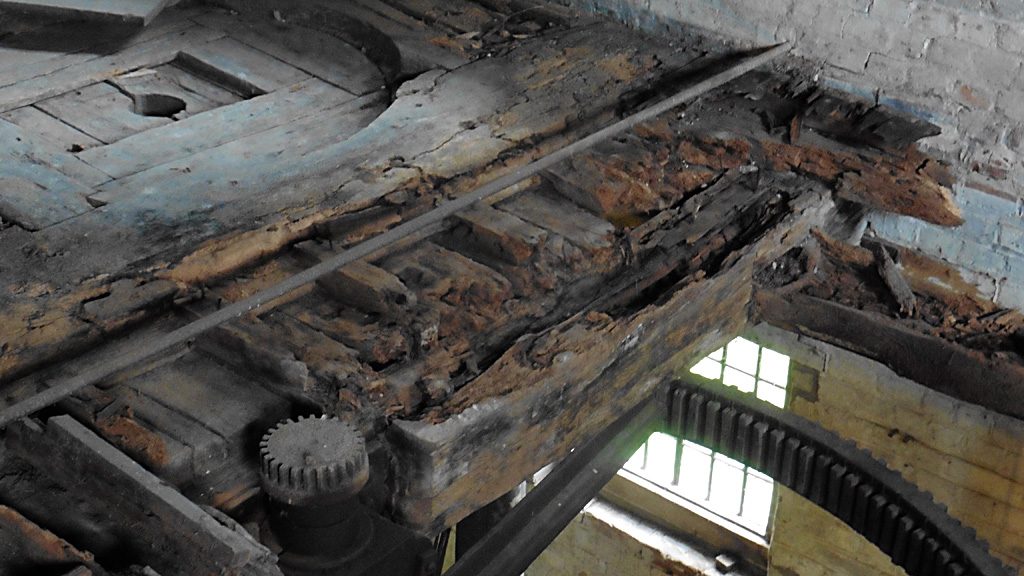
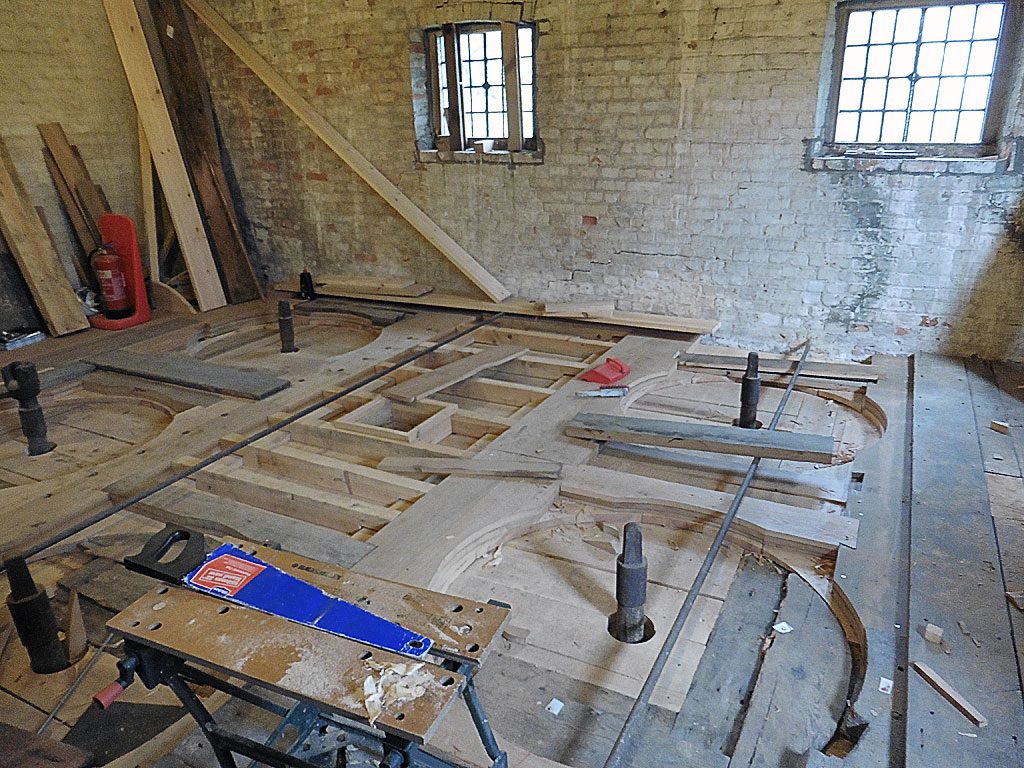
The original floor had a row of coach bolts inserted through kerbs C2 and C10 all the way through the base beams. Most of the original coach bolts through C2 had been lost along with that kerb. The original coach bolts through C10 had been recovered and were still serviceable. Holes were drilled through C10 towards the end of October and the bolts were reinstalled in early November.
In the second half of November new floorboards 29 and 30 were cut but not laid due to the work around position 1 and 2 finishing the cross kerbs. A frame was also made around the hole in the floor for the vertical shaft (visible in the photo above right). This is designed to accept a Perspex window or similar in the future for visitor safety.
Early in December the scaffold structure under the floor was dismantled. This had been kept through 2018 to store new timber on within the mill rather than outside. The “joists” were fixed down to align with the floor board pattern and boards 29 and 30 were laid, but not fixed. New coach bolts with handmade square nuts to match the original design were installed through kerb C2 in the same arrangement as kerb C10.
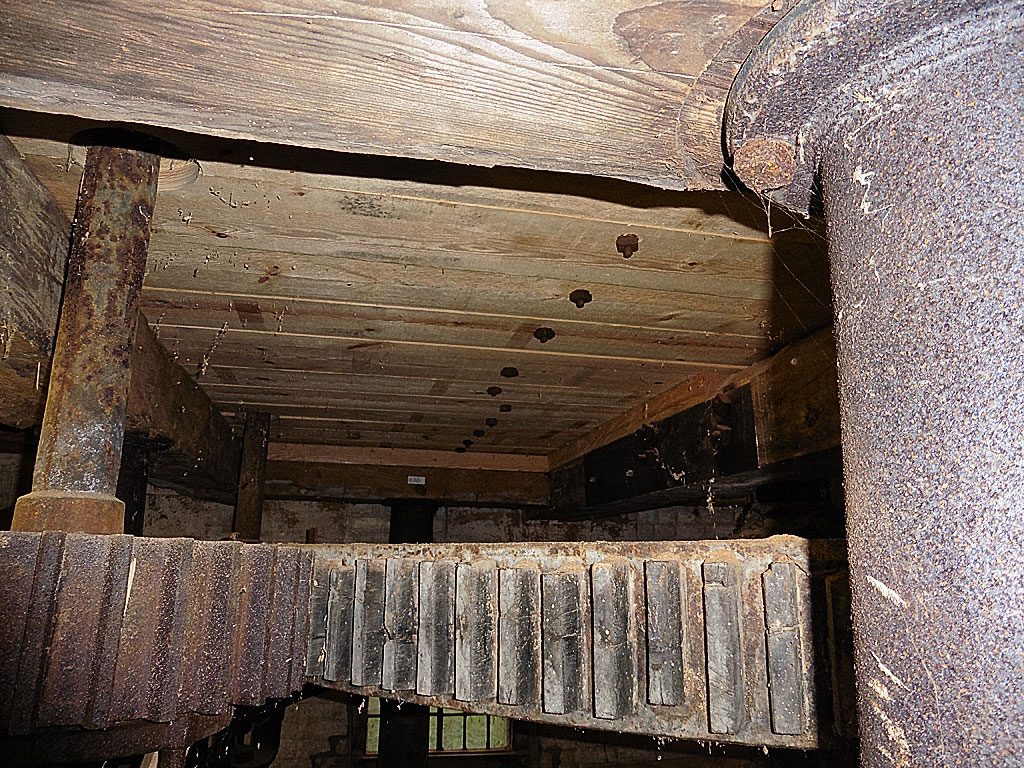
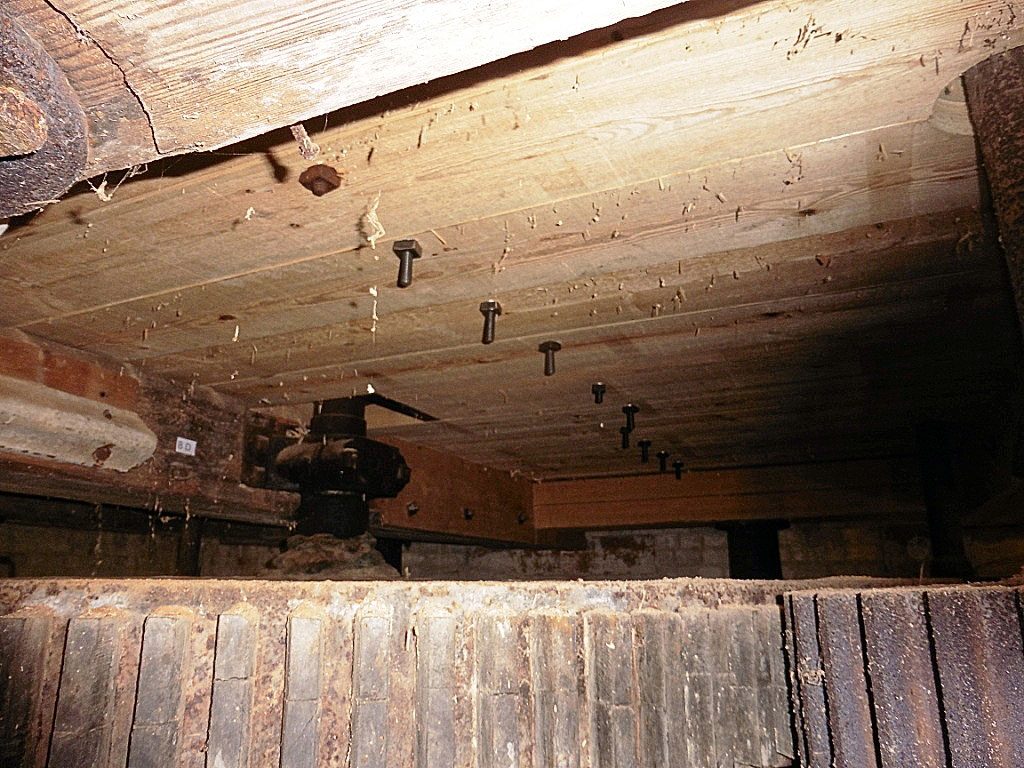
Early in January 2019 the final planks were laid to complete the main flooring, leaving the fiddly boards around each stone position to be done. Once these two planks were laid all the floorboards were screwed down. Attention then turned to the boards that were to frame each stone position.
While one pair of volunteers worked on the floorboards around positions 4 and 5 another pair started installing the planks that formed a disc under each bed stone. About two thirds of the original “under stone” planks were reusable, although many needed repairs due to splitting. Where original planks had either been missing or the original had not been reusable replacement planks were cut. In a few cases a plank was cut from the remains of an old floorboard that had not been good enough to reuse as a floorboard, so that the surface appearance of the repaired plank looks similar to the original.
This work continued through February 2019 and the final planks were laid for position 1 – where the major hole in the floor had been – in the last work session of February. On March 12th 2019, Tim Howson, Maldon District Council Conservation Officer visited the mill to see the completed repairs. Joe Bispham also visited at the same time and saw the finished floor for the first time. Both were pleased with the result and Joe Bispham later said the group had done a brilliant job.
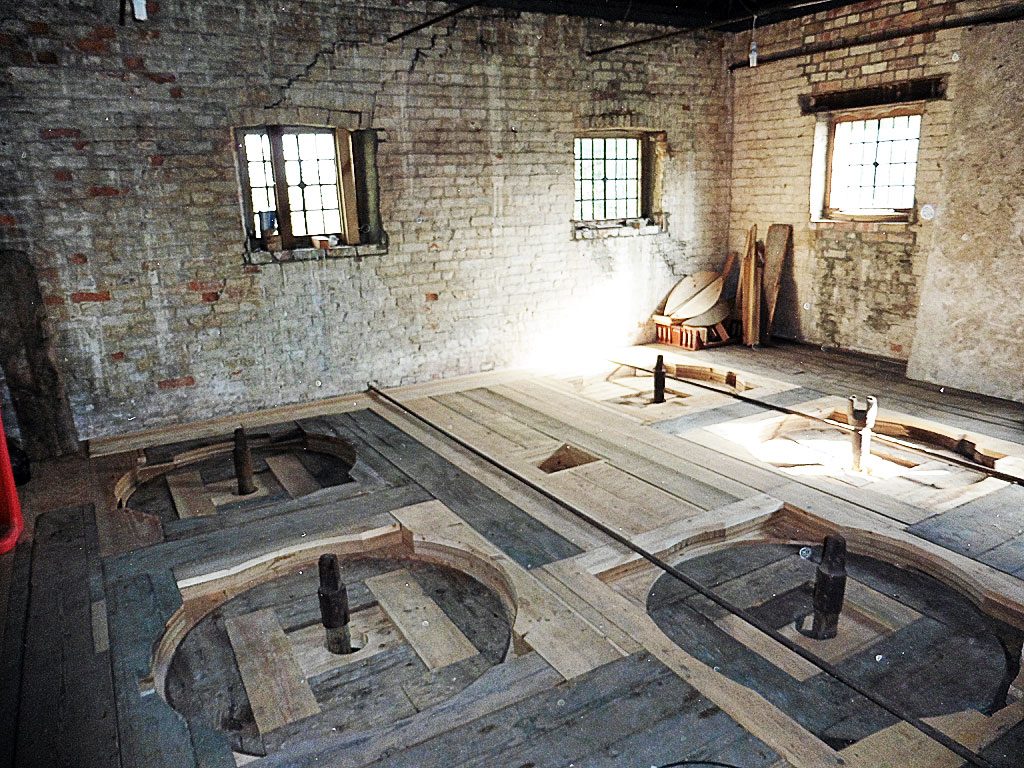
A large number of volunteers have worked on this project and our thanks go to them for giving their time and using their skills to such good effect. Our thanks also go those members of the group and the public who donated cash to get us started and to the Essex Heritage Trust, The Association of Industrial Archaeology and the Society for the Preservation of Ancient Buildings who gave us grants, which paid for the bought in work and materials.
Currently work is progressing on the design and construction of a cut away section of a tun, dummy mill stones and associated equipment.